
Industries
PITERION is widely established across Europe and increasingly active in the US/Canada as well as in the Asia-Pacific region. Our global talent pool and the ability to handle various regulations and market demands allow us to succeed across multiple industries.
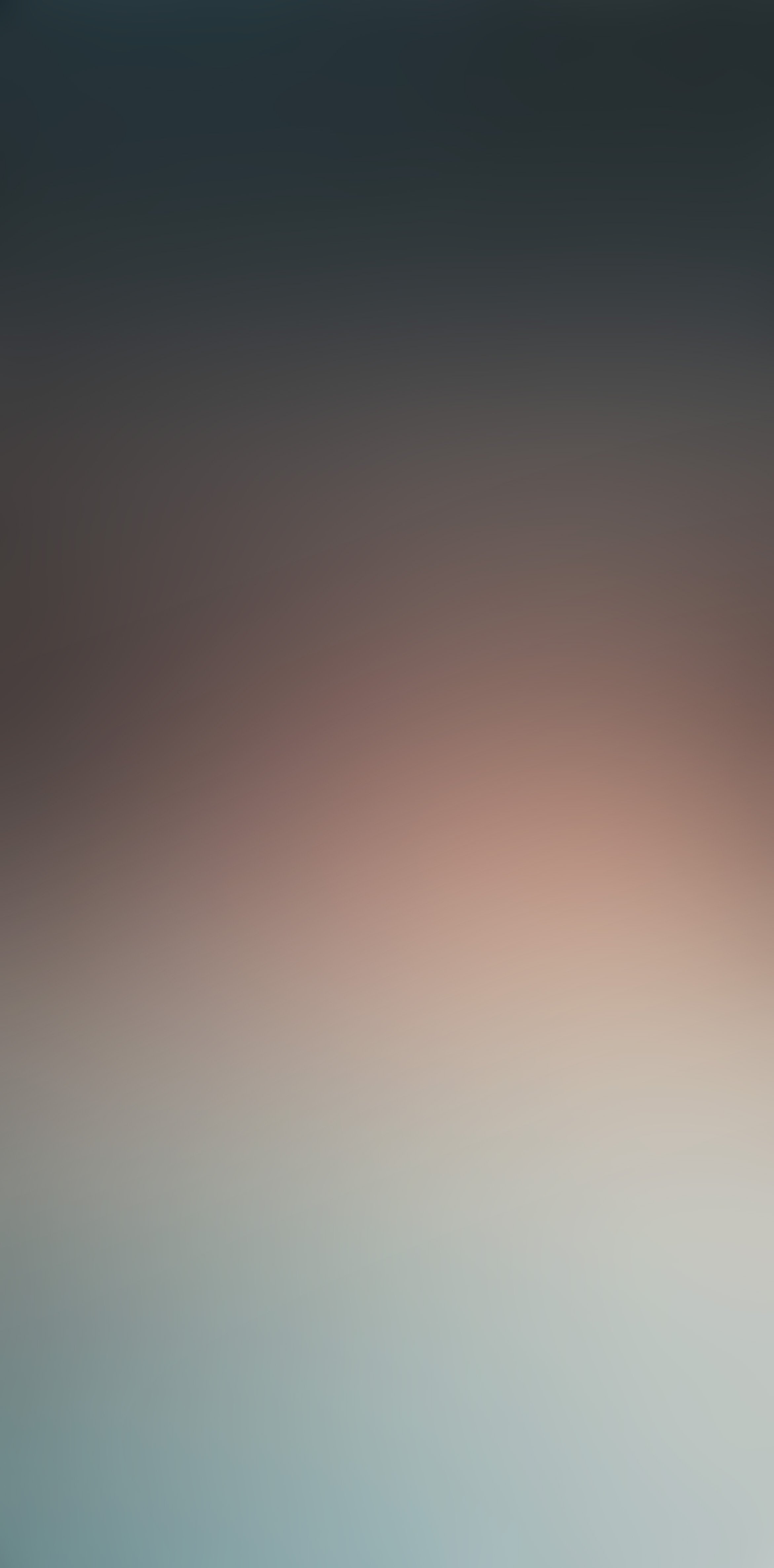
Automotive & Transportation
Software Defined Vehicle and E/E Integration: The increasing software content in vehicles calls for robust ALM solutions.
Model-Based Systems Engineering (MBSE): Simulation-driven, function-oriented development helps to shorten R&D cycles.
Case Example: The development of a product and sales configurator for a global commercial vehicle company led to a 40% reduction in configuration errors.
Aerospace & Defense
Certifications: Adherence to EN 9100 and ITAR/EAR ensures compliance with international supply chain standards.
Digital Twin: Simulation of aircraft components across their lifecycle, seamlessly integrated into product lifecycle management systems.
Reference Project: Modernizing a CAD and PLM environment for a military helicopter manufacturer by consolidating multiple systems into a unified landscape.
Industrial Equipment & Machinery
MBOM/EBOM Linking: Often different BOM views; we enable end-to-end traceability and simplify supplier integration.
Part Centric Design: As a partner, we integrate agile PDM solutions for quick prototyping of mechanical components.
Case Study: Migrating CAD and PLM data from a legacy system to SAP PLM. Result: 20% reduction in maintenance effort, improved data quality.
Pharma & Life Sciences
Regulatory Requirements: Compliance with FDA 21 CFR Part 11, EU-GMP Annex 11, and GxP standards.
ALM & Validation: Utilizing an ALM solution to manage validation documentation, requirements, and test traceability.
Success Example: Implementing a quality and compliance system integrated with MES for a medical technology manufacturer, significantly reducing product introduction timelines despite stringent regulations.
High-Tech & Electronics
Fast Product Cycles: Rapid innovation requires lean PLM processes, agile ALM, and DevOps methods.
Sales Configurators: Complex variants in chips or embedded systems demand smart tools that connect BOM, EBOM, and Software BOM (SBOM).
Reference: A cloud deployment on Azure for traceability of products throughout the production.
Automotive & Transportation– Accelerating Innovation through Digital Transformation
01/ Industry Overview & Current Challenges
The Automotive & Transportation sector is undergoing a profound shift: vehicles are no longer just mechanical machines but highly sophisticated, software-driven systems. As technology and consumer demands evolve at breakneck speed, manufacturers and suppliers must balance electrification, autonomous features, connectivity, and sustainability—all while staying cost-competitive.
Key Challenges:
1.Software-Defined Vehicles(SDVs)
Modern vehicles incorporate complex software ecosystems, from infotainment and driver-assistance functions to remote diagnostics.
Managing firmware updates, over-the-air (OTA) patches, and security standards becomes a strategic priority to keep vehicles both up-to-date and safe.
2. E/E Integration
The shift toward electric and electronic (E/E) architectures requires well-orchestrated design processes, ensuring that mechanical, electrical, and software elements remain seamlessly integrated.
Cross-domain collaboration is paramount, given that new features (e.g., ADAS, autonomous driving) rely heavily on real-time data exchange between sensors, control units, and software layers.
3. Model-Based Systems Engineering (MBSE)
As the complexity of vehicle systems grows, traditional engineering methods struggle to keep up with iterative changes in functionality.
MBSE enables simulation-driven, function-oriented development, helping teams explore different design trade-offs earlier and shorten R&D cycles.
4. Global Supply Chain & Compliance
Automotive companies operate extensive supplier networks. This introduces multiple data formats, version control issues, and potential quality risks if not managed carefully.
Regulatory pressures—like Euro 7 emissions standards or ISO 26262 for functional safety—demand transparent documentation and robust testing procedures.
5. Ever-Increasing Consumer Demands
Car buyers expect rapid innovation: new models, advanced connectivity features, and intuitive in-vehicle experiences.
Manufacturers need flexible production lines and agile planning to bring new variants to market quickly while maintaining brand consistency.
02/ Digitalization Opportunities with ALM & MBSE
Application Lifecycle Management (ALM) and Model-Based Systems Engineering (MBSE) serve as the cornerstones of a modern automotive development strategy. When integrated effectively, these solutions help:
1. Streamline Software Development & Updates
ALM platforms provide full visibility over software requirements, test cases, and bug tracking.
With software becoming a key differentiator in vehicles, the ability to roll out timely updates is essential to remain competitive.
2. Enable System-Level Modeling
MBSE frameworks unify mechanical, electrical, and software components in a virtual environment.
Early-stage simulations can validate design choices, reduce costly errors, and foster cross-functional alignment from the get-go.
3. Improve Cross-Team Collaboration
Engineers, developers, and production planners work off a single source of truth, preventing miscommunication and version mismatches.
Shared data repositories support real-time updates, ensuring that even globally distributed teams can function cohesively.
4. Enhance Traceability & Compliance
Integrated ALM/MBSE solutions document design rationales, change histories, and test outcomes automatically
This proves invaluable for ISO 26262 certification (functional safety) or other regulatory audits, reducing manual overhead.
5. Accelerate Innovation
With robust lifecycle management in place, R&D teams can focus on developing new vehicle functions—like advanced driver-assistance systems—without being bogged down by administrative tasks.
Rapid prototyping and digital twins encourage iterative improvements, helping to bring cutting-edge features to market faster.
03/ Detailed Case Example: Global Commercial Vehicle Configurator
Client Profile:
Focus: Commercial vehicle manufacturer operating across Europe, North America, and select Asian markets.
Situation: Our client saw a surge in demand for highly configurable fleets—ranging from delivery vans to heavy-duty trucks with varied powertrains and cargo options. However, their existing sales process was error-prone, relying on outdated spreadsheets and manual cross-checking.
Business Challenge:
Inefficient Quoting & Ordering: Each new vehicle order required multiple rounds of back-and-forth between sales teams, engineering, and production planners.
Frequent Errors: Mismatches in engine types, chassis configurations, and optional add-ons led to a high rate of rework and dissatisfied customers.
Complexity in E/E Architecture: As our client introduced new electric and hybrid models, the existing manual approach to specifying electrical components exacerbated confusion.
Project Approach:
1. Requirements Definition
PITERION consultants analyzed our clients product portfolio, identifying critical attributes (e.g., wheelbase lengths, engine variations, cabin types) that needed standardized representation.
2. Design & Implementation of a Product & Sales Configurator
We integrated an ALM system to manage the configurator’s software logic—ensuring consistent rules for matching mechanical and electrical sub-systems.
MBSE practices helped align mechanical frames, battery/electrical architectures, and optional software packages (e.g., telematics) in a single model.
3. Cross-Functional Integration
Sales teams entered customer requests via a user-friendly interface, which validated configurations in real time.
The configurator automatically updated BOMs in the PLM system, flagged any incompatible features, and provided accurate cost estimates.
4. Testing & Validation
Before the configurator was fully deployed, PITERION facilitated multiple test cycles involving sales staff, engineering leads, and production managers.
Data from these tests fed back into ALM, refining the business rules for specific scenarios—like operating in extreme climates or specialized cargo requirements.
Results & Impact:
40% Reduction in Configuration Errors: With an automated validation layer, OmniTrak drastically cut the number of incorrect or incomplete orders.
Faster Time-to-Quote: Sales representatives could instantly generate proposals, slashing lead times from weeks to days and boosting customer satisfaction.
Streamlined E/E Development: By linking the configurator to MBSE models, software and hardware teams had a clear view of interdependencies, improving collaboration and reducing rework during production runs.
Enhanced Global Footprint: The client rolled out the solution to dealers in multiple continents, ensuring consistent quoting standards and brand experience worldwide.
Ready to drive your digital transformation forward?
Contact us today and let’s shape the future of mobility together
04/ Conculusion
As the Automotive & Transportation industry enters an era of software-defined vehicles and complex E/E architectures, ALM and MBSE become more crucial than ever. They provide the robust foundation needed to coordinate rapid innovation, ensure compliance with evolving safety and emissions regulations, and enable flexible manufacturing.
At PITERION, we’ve witnessed firsthand how well-implemented, integrated PLM, ALM, and MBSE solutions can propel automotive businesses to new heights of efficiency, quality, and customer satisfaction. From building sophisticated vehicle configurators to orchestrating full digital twins for next-gen electric models, our experts combine deep technical know-how with strategic insights—ensuring your organization stays on the cutting edge of automotive innovation.
Aerospace & Defense – Elevating Mission-Critical Operations through Digital Transformation
01/ Industry Overview & Current Challenges
The Aerospace & Defense (A&D) sector operates under some of the most demanding conditions worldwide—balancing cutting-edge innovation, safety and reliability, and strict regulatory compliance. From commercial aircraft to military helicopters, global supply chains intertwine, and any disruption or design flaw can lead to significant financial losses or even risks to human life.
Key Challenges:
1. Stringent Certifications & Regulations
Adhering to EN 9100 standards ensures quality management across design, development, and manufacturing, while ITAR/EAR compliance governs the export and transfer of defense-related technologies.
Failure to maintain such strict governance can result in heavy fines, reputational damage, or restricted market access.
2. Global Supply Chains & Complex Collaborations
Many A&D projects involve multiple tiers of suppliers around the world. Ensuring that each participant meets regulatory requirements and quality benchmarks is a monumental task.
Inconsistent data formats or misaligned processes can introduce risks—delays, cost overruns, or compromised component quality.
3. High-Risk Engineering & Reliability
Aerospace systems (e.g., avionics, propulsion) often push the boundaries of physics and materials science. Design errors can carry dire safety consequences.
Verifying and validating components demand rigorous simulation, testing, and impeccable traceability from inception to retirement.
4. Digital Twin & Lifecycle Integration
The rise of digital twins—virtual replicas of physical aircraft or defense systems—requires consistent, real-time data from multiple platforms (PLM, MES, IoT sensors).
Legacy methods or disconnected tools may not support the robust integration needed for advanced simulations or predictive analytics.
5. Long Product Lifecycles
Aircraft and defense platforms can remain in service for decades, necessitating continuous updates, retrofits, and maintenance.
Sustaining a coherent digital thread over such an extended timeframe is challenging without robust product lifecycle management.
02/ Digitalization Opportunities with PLM & Digital Twin
Product Lifecycle Management (PLM) platforms, combined with Digital Twin technologies, offer game-changing possibilities to streamline operations and enhance reliability:
1.Seamless Certification Management
A unified PLM environment automates documentation, manages revisions, and supports structured approvals for EN 9100 and ITAR/EAR compliance.
Electronic signatures and audit trails reduce the administrative burden, enabling faster, more transparent regulatory submissions.
2. End-to-End Traceability & Quality Assurance
Integrated PLM solutions link every component to its design specs, manufacturing processes, and service records.
If a part or subsystem fails, root-cause analysis and recalls become more targeted, minimizing downtime and financial impact.
3. Digital Twin for Complex Systems
Simulation-driven models replicate real-world conditions—stress, temperature, aerodynamic forces—across an aircraft’s lifecycle.
Engineers can predict maintenance needs or design flaws early, optimize fuel efficiency, and reduce operational costs.
4. Global Collaboration & Supply Chain Alignment
Integrated ALM/MBSE solutions document design rationales, change histories, and test outcomes automatically.
This proves invaluable for ISO 26262 certification (functional safety) or other regulatory audits, reducing manual overhead.
5. Lifecycle Upgrades & Retrofits
Data captured in the PLM system supports efficient retrofits—whether updating cockpit avionics or integrating new materials for weight reduction.
With a digital twin, teams can quickly evaluate how proposed modifications will impact overall aircraft performance and safety compliance.
03/ Reference Project: Modernizing a CAD & PLM Environment for a Military Helicopter Manufacturer
Overview:
A leading military helicopter manufacturer faced the challenge of operating multiple CAD and PLM solutions inherited through acquisitions. Each site had its own workflows, creating compliance hurdles and high maintenance costs. A unified approach was essential to support global collaboration, ensure ITAR/EAR adherence, and reduce operational complexity.
Project Approach:
Assessment & Roadmapping
Specialists analyzed the existing systems and workflows, identifying redundancies and potential risk points.
A clear roadmap was developed to consolidate CAD repositories and unify PLM modules, integrating compliance checkpoints throughout.
System Consolidation & Upgrade
The scattered CAD environments (including various legacy solutions) were merged into a modern PLM suite.
Advanced data migration tools ensured minimal downtime; part data, drawings, and revision histories were migrated with comprehensive traceability.
Integration with Digital Twin Capabilities
A Digital Twin framework was introduced for advanced simulations of rotor dynamics, structural stress, and environmental condition.
The framework drew real-time data from the newly consolidated PLM system, ensuring accurate modeling for prototypes and fielded aircraft.
Automated Compliance Workflows
ITAR/EAR requirements were embedded into the PLM environment, ensuring role-based access control and automated export documentation.
Electronic approvals replaced paper-based sign-offs, reducing cycle times and mitigating audit risks.
Results & Impact:
Unified PLM & CAD Landscape: The consolidation lowered system maintenance costs by approximately 30%.
Faster Design Cycles: Engineering teams completed design iterations more rapidly, with data discrepancies virtually eliminated.
Streamlined Regulatory Adherence: Centralized audit trails and automated export controls simplified compliance during government inspections.
Future-Ready R&D: Digital Twin capabilities allowed for more sophisticated simulations, including edge-case stress testing, resulting in safer, more reliable helicopter designs.
Looking to transform your aerospace or defense projects?
Contact us to explore how an integrated PLM and Digital Twin approach can future-proof your operations.
04/ Conculusion
Aerospace & Defense organizations operate under intense scrutiny and must meet rigorous safety and compliance standards. Adopting a unified PLM system in tandem with Digital Twin methodologies not only standardizes operational excellence but also lays a strong foundation for ongoing innovation—spanning the entire lifecycle of aircraft and defense systems.
At PITERION, our team helps A&D companies seamlessly integrate advanced tools and workflows, from CAD consolidation to ITAR/EAR compliance automation. Combining our deep industry expertise, vendor-neutral integrations, and proven best practices enables your enterprise to streamline collaboration, cut time-to-market, and fortify mission-critical reliability—all while meeting the demanding standards of modern aerospace and defense.
Industrial Equipment & Machinery – Driving Efficiency Through Unified Product Data Management
01/ Industry Overview & Current Challenges
The Industrial Equipment & Machinery sector is at the forefront of global manufacturing, catering to diverse markets such as construction, mining, automation, and robotics. These products often feature high levels of customization, intricate supply chains, and extended operational lifespans. Effective data management and streamlined processes are therefore pivotal for achieving sustainable growth and customer satisfaction.
Key Challenges:
Complex BOM Management
Multiple views of the Bill of Materials (BOM)—engineering (EBOM), manufacturing (MBOM), and service (SBOM)—can easily lead to data silos.
Ensuring that these BOMs remain synchronized across departments is critical for accurate production planning, inventory control, and after-sales support.
High Degree of Customization
Many manufacturers operate on build-to-order or engineer-to-order models, resulting in numerous part variants and configurations.
Without a robust data management strategy, tracking each variant can become error-prone, cause project delays, and inflate costs.
Global Supply Chain & Supplier Integration
Sourcing components from multiple vendors worldwide requires aligning different IT systems, part numbers, and revision protocols.
Even a single mismatch in data exchange can lead to considerable production delays or quality issues.
Legacy Systems & Fragmented Data
Rapid growth or mergers often leave organizations with outdated CAD and PLM platforms that no longer support modern requirements.
Migrating to a unified environment may seem daunting, but it is essential for consistent processes and data integrity.
Extended Product Lifecycles
Industrial machinery can remain in service for 10–20 years or longer, making it vital to track upgrades, retrofits, and part replacements over a product’s entire lifespan.
Without a comprehensive product data management approach, ensuring consistent documentation and compliance becomes difficult.
02/ Digitalization Opportunities: MBOM/EBOM Linking & Part-Centric Design.
MBOM/EBOM Linking
Unified Visibility: Synchronizing engineering BOMs (EBOM) with manufacturing BOMs (MBOM) provides a comprehensive view of every product—from concept through production.
Streamlined Changes: Automated notifications and version control help ensure that alterations in design are reflected in manufacturing instructions, cutting rework and lead times.
Supplier Integration: Aligning BOM data also facilitates communication with suppliers, keeping critical specifications and revisions consistent across the supply chain.
Part-Centric Design
Quick Prototyping: Agile product data management (PDM) methods enable teams to rapidly iterate mechanical components, virtually test them, and finalize updated designs without losing revision history.
Centralized Parts Library: By unifying parts data in a single repository, duplication can be avoided, standard naming conventions enforced, and collaboration improved between engineers and supply chain teams.
Collaboration & Traceability: Design, procurement, and production stakeholders share a single source of truth, ensuring alignment on part specifications and reducing operational errors.
03/ Case Study: Migrating CAD & PLM Data to a Modern Platform
Context & Objectives
A mid-sized industrial machinery manufacturer relied on a homegrown product data management system, alongside multiple fragmented CAD solutions. This setup caused BOM inconsistencies, high maintenance costs, and difficulties in integrating new suppliers. Recognizing these challenges, the company decided to consolidate its data into a modern, enterprise-grade PLM environment to standardize part naming, streamline collaboration, and enhance supplier communication.
Challenges
Data Fragmentation: Design files and metadata were spread across different file structures, each with its own naming rules.
Limited Traceability: Changes made in engineering were not automatically reflected in downstream manufacturing, resulting in production errors.
High Maintenance Overhead: Maintaining legacy code and infrastructure consumed excessive resources, detracting from core business needs.
Project Approach:
1.Assessment & Strategy
Project teams audited the existing CAD models, BOM structures, and metadata to identify redundancies and inconsistencies.
They formulated a phased migration plan to retire the legacy system while minimizing disruption to active projects
2. Data Cleansing & Mapping
Duplicates, outdated versions, and incomplete assemblies were either merged or removed.
Clear mapping rules were established to align naming standards and part revisions with the new PLM structure, reducing the risk of data loss.
3. Pilot Migration & Training
A pilot run with a single product line allowed engineers and supply chain teams to become familiar with new workflows.
Feedback gathered from this pilot was used to refine migration scripts and user training materials.
4. Full-Scale Rollout
With lessons from the pilot, the remaining CAD and PLM data was migrated in a series of well-defined waves.
An internal support team provided ongoing training and troubleshooting, ensuring successful user adoption.
Results & Impact:
20% Reduction in Maintenance Effort: Decommissioning the legacy system and consolidating resources onto the new platform lowered IT overhead significantly.
Improved Data Quality: A centralized data repository resolved recurring BOM misalignments, ensuring consistent part and assembly records.
Enhanced Collaboration: Unified dashboards and version tracking improved communication among design, procurement, and manufacturing teams.
Future-Ready Foundation: With a modern, scalable system in place, the organization can more easily integrate new suppliers, adopt emerging technology (such as IoT sensors), and manage global product lines efficiently.
Curious about how you can optimize BOM management and strengthen your global supply chains?
Get in touch to learn more about our solutions for the industrial machinery sector.
04/ Conculusion
In the Industrial Equipment & Machinery space, success hinges on the ability to effectively manage product data while accommodating diverse BOM structures and global supply networks. By linking MBOM with EBOM, companies can bridge the gap between engineering and production, enhancing efficiency and reducing time-to-market. Adopting part-centric design with agile PDM solutions further streamlines collaboration and speeds up product iteration.
At PITERION, we help organizations navigate these transitions through vendor-neutral strategies that address legacy environment modernization, data migration, and next-level integration. With our deep expertise and proven methodology, your enterprise can confidently upgrade to a unified, high-performing environment—ready to embrace the challenges and opportunities of tomorrow’s industrial manufacturing landscape.
Pharma & Life Sciences – Streamlining Innovation Under Strict Compliance
1/ Industry Overview & Current Challenges
The Pharma & Life Sciences sector is among the most tightly regulated industries globally. From drug development and manufacturing to medical device engineering, organizations face high stakes for patient safety, quality control, and legal compliance. Implementing robust digital solutions is not just an efficiency move—it’s essential for long-term viability and public trust.
Key Challenges:
1. Stringent Regulatory Requirements
Companies must comply with regulations such as FDA 21 CFR Part 11, EU-GMP Annex 11, and various GxP standards.
Non-compliance can lead to severe penalties, product recalls, or even loss of market authorization.
2. Complex Validation & Documentation
Pharma and medtech products undergo rigorous testing and validation at each stage of development.
Managing validation protocols, test cases, and audit trails can be overwhelming without structured workflows and centralized data repositories.
3. Extended Product Lifecycles & Traceability
From clinical trials to post-market surveillance, product lifecycle management can span many years, requiring robust version control and historical data retention.
Ensuring every change is traceable and fully documented is imperative for regulatory audits and patient safety.
4. Global Collaboration
Many life sciences companies operate across multiple regions, each with its own regulatory landscape.
Distributed teams must maintain consistent quality standards while also localizing products for diverse markets.
5. Data Integrity & Security
Sensitive intellectual property, patient data, and manufacturing details must be protected against leaks or unauthorized access.
Data integrity issues, such as incomplete audit trails or inaccurate test results, can halt clinical trials and jeopardize approvals.
2/ Digitalization Opportunities: ALM & Validation
A well-defined Application Lifecycle Management (ALM) framework can be transformative for Pharma & Life Sciences organizations, especially regarding validation, test documentation, and compliance reporting:
1. Comprehensive Validation Management
ALM solutions offer end-to-end traceability of requirements, test cases, and defect tracking.
Automating validation workflows allows teams to systematically document every step—facilitating smoother audits and lowering human error risks.
2. Electronic Records & Signatures
Incorporating e-signature capabilities ensures alignment with regulations like 21 CFR Part 11, reducing reliance on paper records and manual approvals.
Real-time data capture enables quicker response to deviations or anomalies during trials or manufacturing.
3. Requirements & Test Traceability
ALM platforms link user requirements, functional specifications, and test procedures in one unified environment.
Teams can quickly pinpoint the source of any issue (e.g., a failed test or out-of-spec result), accelerating corrective actions and ensuring compliance.
4. Seamless Integration with Other Systems
Tying ALM to PLM, MES, or ERP solutions ensures that production updates and new formulations automatically trigger corresponding validation steps.
This holistic approach breaks down silos, enabling cross-functional teams—R&D, manufacturing, quality—to share data seamlessly.
5. Streamlined Regulatory Submissions
Generating the necessary documentation for submissions or audits becomes more straightforward when validation records and version histories are centrally managed.
Digital sign-offs and automated reporting cut both time and administrative burden.
3/ Success Example: Quality & Compliance System Integrated with MES
Challenges
Regulatory Hurdles: Frequent updates to industry guidelines made it difficult to keep validation practices current and fully compliant.
Manual Documentation: Paper-based processes led to approval delays and higher risk of human error.
Limited Integration: Manufacturing systems weren’t synced with validation records, causing repeated data entry and bottlenecks.
Project Approach:
1.Assessment & Planning
A cross-functional team mapped existing validation workflows, identifying bottlenecks and gaps in test traceability.
A phased plan was introduced to replace manual logs with a digital ALM system that included built-in compliance checks.
Context & Objectives
A medical technology manufacturer sought to accelerate product introduction timelines without compromising regulatory compliance. Their existing workflow relied on multiple spreadsheets, manual paper logs for validation, and disconnected manufacturing systems—each operating in a silo.
2. Implementation of a Quality & Compliance System
The ALM was configured to enforce electronic signatures and secure audit trails aligned with 21 CFR Part 11.
Validation documentation, risk assessments, and SOPs were digitized, allowing authorized personnel to track progress in real time.MES Integration
Manufacturing data—such as batch records, equipment logs, and process parameters—was linked to validation steps in the ALM.
Deviations triggered automated notifications, prompting immediate review and corrective action.
3. Training & User Adoption
Interactive sessions guided quality teams and production managers through new workflows, ensuring minimal disruptions.
A dedicated support channel resolved user queries, fostering a smoother transition to digital operations.
Outcomes & Impact
Significant Reduction in Product Introduction Timelines: Eliminating manual approvals and synchronization delays allowed new devices to reach the market faster, even under tight regulatory constraints.
Enhanced Compliance: The electronic validation framework streamlined audits; regulators received clear, real-time evidence of adherence to GxP standards.
Lower Risk of Errors: Automated logs and cross-referenced test data greatly reduced the chance of missing documentation or skipping crucial validation steps.
Improved Scalability: With a robust digital foundation, the company easily accommodated new product lines, additional manufacturing plants, and evolving regulations.
Ready to streamline your validation process and shorten time-to-market?
Reach out to our team and let’s chart a path to smart, future-ready Pharma & Life Sciences solutions.
4/ Conculusion
In Pharma & Life Sciences, success hinges on striking the right balance between innovative product development and unwavering compliance. By implementing a well-structured ALM system and integrating it with production environments, organizations can seamlessly manage validation, tighten traceability, and adapt swiftly to changing regulations.
At PITERION, we combine our industry insights with advanced digital strategies to help you implement tailored, compliant, and scalable solutions. Whether your goal is to accelerate clinical development or improve quality control in manufacturing, our vendor-neutral approach ensures a smooth transition into a new era of efficient, compliant operations.
High-Tech & Electronics – Accelerating Innovation with Agile Product Lifecycle ManagemenT
1/ Industry Overview & Current Challenges
The High-Tech & Electronics sector is defined by rapid innovation, intense competition, and the ever-growing sophistication of chips, circuits, and embedded software. Product lifecycles often last mere months, demanding continuous development of new features and frequent product refreshes. Achieving sustainable success in this environment calls for lean PLM processes, agile ALM approaches, and modern DevOps practices that can swiftly adapt to evolving market demands and technology trends.
Key Challenges:
1. Fast Product Cycles
Companies race to introduce new devices and components, from wearables to advanced sensors, pushing the limits of engineering teams.
Maintaining product quality and reliability under tight time constraints requires a robust digital thread—where design data, production details, and software revisions remain fully integrated.
2. Complex Embedded Systems
High-Tech products often combine mechanical, electrical, and software elements into a single tightly coupled unit (e.g., IoT devices, telecom modules, consumer electronics).
Traditional siloed product development methods can lead to version mismatches, costly rework, and delayed market entry.
3. Sales Configurators for Advanced Variants
Chips and embedded systems frequently come in numerous variants, each with different core speeds, memory configurations, or specialized firmware.
Handling these variations manually is prone to errors; advanced configurator tools are vital for connecting BOM, EBOM, and the Software BOM (SBOM).
4. Rapid Change Management
Electronic components can go through multiple iteration cycles in quick succession, requiring a flexible process for capturing design changes and pushing updates to production lines.
Failing to manage version control properly can result in supply chain disruptions or, worse, flawed products reaching customers.
5. Data Integrity & Security
Many High-Tech firms rely on contract manufacturers or have distributed R&D centers worldwide. Harmonizing design specs, production details, and quality checkpoints across continents can be challenging without a unified platform.
2/ Digitalization Opportunities: Lean PLM, Agile ALM & DevOps
1.Lean PLM for Dynamic Product Launches
A streamlined PLM approach focuses on minimal waste and fast iteration cycles. Key features include real-time collaboration among design, engineering, and manufacturing, as well as automated workflows for approvals and change orders.
Linking core engineering data (EBOM) to manufacturing data (MBOM) ensures that new product variants are documented thoroughly, minimizing launch delays and rework.
2. Agile ALM for Software-Driven Innovation
Modern ALM solutions break down complex firmware or embedded software projects into manageable sprints, enabling iterative testing and continuous integration.
DevOps practices—such as automated builds, containerization, and rapid feedback loops—ensure that software updates or patches can be safely deployed without halting critical operations.
3 .Integrated Sales Configurators
In High-Tech & Electronics, customizing chipsets or embedded modules might involve toggling dozens of parameter options. Sales configurators that draw from a single source of truth—combining mechanical, electrical, and software BOMs—help avoid incorrect orders and reduce time spent on manual validation.
These systems also streamline quotes, pulling precise cost and component data from a unified repository, boosting both speed and accuracy in sales engagements.
4 .Real-Time Traceability & Compliance
With product cycles so short, any slip in compliance or quality can damage brand reputation. Integrating PLM and ALM solutions with cloud-based analytics ensures real-time visibility into production status and potential issues.
Teams can track each unit’s history down to its firmware version, facilitating faster recalls or pinpointing defective batches if something goes awry.
3/ Reference: Cloud Deployment on Azure for Product Traceability
Context & Objectives
A rapidly growing electronics manufacturer sought to improve traceability across all production phases, from initial design to final assembly. Their existing method relied on a patchwork of legacy systems, spreadsheets, and email threads to track version changes—a bottleneck that hindered the company’s ability to deliver on tight schedules and adapt to evolving customer demands.
Challenges
Fragmented Data Storage: Different teams held component and firmware updates in separate repositories, causing confusion over which design version to use.
Limited Visibility: Managers lacked a single dashboard view to see real-time production statuses, making it difficult to spot potential defects or shortages early.
Short Development Cycles: The company launched new product lines every 6–8 months, leaving little room for manual reconciliation of BOM and SBOM data.
Project Approach:
1.Discovery & Planning
A cross-functional assessment mapped all data flows—mechanical BOMs, electrical schematics, firmware updates—to identify key integration points.
The team drafted a roadmap to modernize data management, introduce agile ALM practices, and unify traceability into one system.
2. Cloud Deployment
The manufacturer chose a cloud-based infrastructure on Microsoft Azure, enabling scalability and global availability.
Specialized connectors were implemented to automate data exchange between design tools, manufacturing execution, and version control systems for software.
3. Traceability & Real-Time Dashboards
A centralized platform linked each product unit’s ID with its BOM, SBOM, and manufacturing milestones.
Real-time dashboards allowed operations and supply chain managers to track unit progress, component usage, and test results. Deviations triggered alerts for immediate remediation.
4. DevOps & Rapid Rollouts
Agile ALM allowed for continuous firmware integration and testing. New software features or bug fixes were containerized and validated in staging environments before final deployment to production.
This iterative approach ensured stable, incremental improvements without compromising ongoing production runs.
Outcomes & Impact
Seamless Traceability: Each unit’s “digital passport”—combining hardware and software lineage—substantially reduced the time needed for audits or recalls.
Increased Agility: By linking engineering changes to production lines in near-real time, the company rapidly introduced product variants, meeting dynamic market demands.
Reduced Errors & Downtime: Automated alerts and dashboards highlighted issues before they escalated, decreasing production rework and QA overhead.
Scalable Cloud Framework: Azure’s flexible architecture provided the foundation for additional expansions, such as advanced analytics, AI-driven quality inspections, and integration of new product lines.
Ready to transform your High-Tech & Electronics processes?
Get in touch and let’s co-create a cutting-edge framework that drives your product innovation forward.
4/ Conculusion
In the High-Tech & Electronics domain, rapid product cycles and complex embedded systems leave little margin for error. By combining lean PLM, agile ALM, and DevOps methodologies, companies can enhance collaboration, manage configuration complexities, and deliver innovative solutions to market at unprecedented speed.
At PITERION, we empower tech-driven enterprises through vendor-neutral PLM/ALM integration, modern cloud deployments, and customized approaches for real-time traceability. Whether you’re introducing new semiconductor variants, rolling out IoT modules, or scaling consumer electronics manufacturing, our expertise in Digital Transformation ensures you remain resilient, quality-focused, and ahead of the competition.